Taiyo Kogyo Column
Explanation of key points in creating a logistics workflow for a company/companies for the purpose of implementing a WMS (Warehouse Management System).
2024.02.07
An increasing number of companies and firms are considering the introduction of a WMS (Warehouse Management System) in order to improve efficiency, productivity, and reduce costs in their often complicated logistics operations.
In implementing a WMS, it may be necessary to start with the creation of the current warehouse workflow, and many may be wondering, “I don’t know how I should create the workflow,” or “I want to know the key points to make the introduction of a WMS smooth. In this article, we will explain the basic workflow of warehouse management as well as the points for creating a workflow to introduce a WMS.
Warehouse workflow needs to be organized to implement a WMS (Warehouse Management System)
WMS (Warehouse Management System) is a system to improve the efficiency of logistics operations, including inventory management in warehouses.
The introduction of a WMS will help solve various on-site problems, such as reducing workload, improving productivity, and preventing human error, by streamlining warehouse operations such as shipping and receiving. It can also reduce costs, improve the quality of warehouse operations, guarantee the quality of goods in stock, and increase customer satisfaction.
Various WMS systems are available as products and services, including cloud-based, packaged, and on-premise systems. It is important to select and use a system that fits your company’s issues and implementation objectives. If you implement a WMS without understanding the issues and objectives of your company, it may not be effective.
In addition, initial and running costs are incurred in implementing and operating a WMS, so it is important to clarify your company’s situation, issues, and the purpose of implementing a WMS, and to introduce an appropriate system.
A review of the warehouse workflow is useful in identifying the company’s issues and clarifying the purpose of introducing a WMS. By creating and visualizing warehouse operations as a flow, issues occurring in the business can be clarified. Such preliminary organization will lead to the selection of a WMS with the functions and features to solve the issues.
Basic Warehouse Management Workflow
This section describes the basic workflow that occurs in warehouse management.
receiving operations
Receiving is the receipt of delivered goods. Confirmation is required that the goods have been received as scheduled. If the goods received or the number of goods received are incorrect, the supplier is pointed out and asked to take action.
warehousing operations
This operation involves storing incoming goods on shelves, pallets, or other necessary locations. There are two main management methods and approaches when receiving goods: fixed location, in which goods are stored on predetermined shelves, and free location, in which goods are stored by specifying any shelf.
In the case of fixed locations, it is important to note that if goods are placed on the wrong shelf, they may not be found when picking, or the wrong goods may be picked up and shipped, resulting in a mis-shipment. In the case of free-location management, it is necessary to control where the goods are stored, so inventory management systems are mainly used for this purpose.
warehousing operations
This is the process of removing goods from the stored shelves for shipment. If location management is in place to control what is stored where, the shelves of the relevant products can be quickly identified, allowing for smooth pickup and delivery. If location control is not in place, you have to remember where each item is kept.
shipping operations
This flow prepares the outgoing goods for delivery and shipping. Shipment inspection is performed to ensure that the goods to be shipped are gathered as scheduled. It is important to note that if shipping inspection is not performed properly, it can cause erroneous shipments.
Workflow issues that can be resolved by implementing a WMS (Warehouse Management System)
The introduction of a WMS (Warehouse Management System) helps to solve various issues in warehouse management operations, and the issues that can be solved by a WMS are explained from the perspective of work flow.
Discrepancy between theoretical and actual inventory numbers
Theoretical inventory is the number of merchandise inventory that is registered and managed in the data. Actual inventory refers to the number of product stock that actually exists in the warehouse. Theoretical inventory and actual inventory must be the same, but some forgetting or error in processing may cause a discrepancy between theoretical inventory and actual inventory.
The main causes of discrepancies between theoretical inventory and actual inventory are errors that occur in the normal course of business, such as forgetting to process incoming goods or processing the wrong number of goods, or shipping the wrong goods or wrong quantities.
Other causes of inventory discrepancies include lost inventory, incorrect inventory counts, and mishandling of non-performing items (damaged, expired, etc.) WMS can centralize these previously visual and manual warehouse operations through barcode processing, preventing discrepancies between theoretical inventory and actual inventory before they occur. This prevents the discrepancy between the theoretical and actual inventory counts in advance.
If there is an error in processing, the WMS will issue an error or warning so that the calculation or administrative values will not be off.
delay in delivery
Delays in delivery may occur due to operational delays in shipping out, loss of inventory, or delays in shipping operations. Delayed delivery, i.e., failure to deliver goods at the time and date requested by the customer, may cause a loss of customer satisfaction and trust. In some cases, the customer may incur significant losses and be forced to cancel the transaction or compensate for the damage.
The WMS also digitally manages shipping and receiving operations, preventing delivery delays due to errors. Because shipping and receiving operations are streamlined, inventory dispatching and product searches are more accurate and can be processed more quickly.
delivery error
This is a mistake in which goods are delivered to the wrong place. A WMS can centralize the input, confirmation, and disbursement of delivery addresses, thereby preventing manual or visual errors.
Points for creating and reviewing work flow for WMS (Warehouse Management System) implementation
In order to introduce a WMS, it is necessary to review the workflow to identify issues occurring in your company and use this information to select a WMS system. This section explains the key points for creating and reviewing the workflow when aiming to introduce a WMS.
Purpose of Business Flow Creation
Warehouse workflow diagrams are created to visualize the flow of work that occurs in warehouse operations. By creating a business flow diagram, it is easier for those who are not directly involved in warehouse operations, such as personnel from other departments or WMS system vendors, to understand the details of various warehouse operations and their detailed flow.
The workflow can also be used to collaborate with other related departments, such as the IT system department and the accounting department, when implementing a WMS, and to receive proposals from the WMS system vendor regarding necessary functions and issues that can be solved for the business in question. The business flow can also help to identify issues that arise in the flow of warehouse operations in your company, leading to the selection of an appropriate WMS system.
Draw an overall diagram and then write out the flow of each task.
First, write down the entire logistics flow that occurs in your company. For example, in the case of a manufacturing company, the flow includes procurement of raw materials, inventory in process, manufacturing of products, and shipping. In the case of a wholesale company, the flow includes purchasing from suppliers, inventory control, and shipping products to customers.
The entire picture is written out in a flow, and then detailed work for each process is written in. For example, for the receiving process, this would include ordering goods, receiving, warehousing, and inventory posting.
Create a concise, serialized flow
There is no specific format for creating a business flow. Any writing style or construction method will work as long as the content can be understood by a third party who is not directly involved in the field and can understand the warehouse operations flow.However, if you include too many details, such as processes that should be grasped by on-site employees, the contents will become too complex and difficult to understand.
Since the work in each process often overlaps in procedure and content, it will be easier to organize the flow in chronological order by creating a serial flow as the main body rather than a parallel flow.
Establish a clear starting point for the workflow.
Whether viewed from the right end or the left end, the work flow is easier to read when it is clear which flow starts where.
Create a logistics-centric view.
When creating a business flow for the purpose of introducing a WMS, consider the flow of goods handled by the company (i.e., logistics) as the center of the flow. By focusing on the flow of goods, the contents of the business flow can be understood at a glance. Conversely, if you do not focus on logistics, you may end up with a flow that is difficult to understand what the flow is about, such as data flow or work flow.
If branching occurs in the workflow, the branching conditions should also be briefly described.
To obtain further benefits of workflow improvement through WMS implementation
This section introduced the workflow that occurs in warehouse operations and how to create a workflow when introducing a WMS. while a WMS has the advantage of improving the efficiency and productivity of warehouse operations, it is important to select a system that meets the issues and objectives. First, create a workflow to understand the issues occurring in your warehouse operations and the purpose of introducing a WMS, and use this information to help you introduce a WMS.
Tent Warehouseへの
Contact us
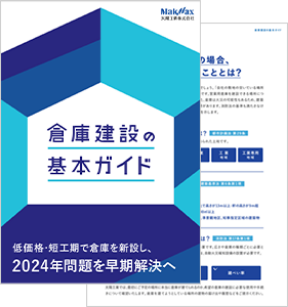
What you need to know when building a warehouse
We packed it all in.
Clues to solving the 2024 problem
I want to build a warehouse in an economical way.
Which type of warehouse should we build?
I want to learn the basics of warehouse construction anyway.
I'm concerned about the 2024 problem, but I don't know what to do about it.
Related Articles
- TOP>
- Taiyo Kogyo Column>
- Explanation of key points in creating a logistics workflow for a company/companies for the purpose of implementing a WMS (Warehouse Management System).