Taiyo Kogyo Column
A management system that solves the problems of logistics warehouses [What are the advantages and disadvantages of WMS implementation?
2024.01.29
Do you think that a warehouse should be able to store goods only? Warehouses must be able to promptly move goods in and out as required. It also needs to be designed to avoid creating unnecessary space. Above all, it must be safe for the workers. This article introduces the WMS (Warehouse Management System), which supports more ideal warehouse operations.
What kind of system is WMS?
WMS is a system that expands the possibilities of warehouses.
WMS to improve warehouse productivity
WMS is an abbreviation for Warehouse Management System. The use of a warehouse varies depending on the type of industry. A mail-order company needs a distribution center to store and ship its products, while a manufacturing company needs two types of warehouses, one for raw materials and the other for pre-shipment products.
Logistics terminals also need to sort packages by destination. Thus, warehouses are used for multiple purposes, but the basic idea is to know exactly where and how many items are in the warehouse. In addition, the WMS can determine the warehouse’s capacity based on unused space. Increasing storage capacity more than ever before will also lead to improved warehouse productivity.
Image of WMS operation
The WMS uses barcodes to manage warehouse shipments. A worker in charge of the operation reads the barcodes with a handy scanner. The read data is managed in a database in the system, and information such as storage location, inventory, product name, and arrival date are all managed together.
When shipping, the system communicates storage locations and picking instructions so that the oldest items with the oldest arrival date are shipped first, so that the items can be shipped promptly without the need to search for them.
What is the difference between a core system or delivery management system and a WMS?
Multiple management systems may be used in the operation of a company. And each system may have similar functionality. This section summarizes the differences between a WMS and non-WMS systems used by companies that use warehouses.
Differences between WMS and core systems
Some mission-critical systems, which are the foundation of a company’s business, also have inventory management functions. Core systems consider inventory as a part of assets. Even if there are multiple warehouses, the system does not distinguish between them, but keeps track of how many yen worth of inventory is held by the entire company.
If there are 10,000 pieces of goods with a cost of 1,000 yen, an asset of 10 million yen is recorded and reflected in the company’s financial statements. While this is useful for understanding the business situation, it does not have much impact on the logistics field.
Difference between WMS and inventory management system (SMS)
Inventory Management System (Stock Management System) is a system to monitor the inventory status of each product and warehouse, as well as the flow of inventory, such as receiving schedule and shipping schedule.
While this is an essential function for buyers to see the turnover rate of products and adjust the number of next shipments and delivery dates, it is not suitable for understanding the storage space in the warehouse or the available space in the warehouse. WMS management enables smooth implementation of efficient production planning, shipping/receiving planning, and warehouse floor space expansion planning.
Differences between a WMS and a shipping management system (TMS)
The main purpose of a Transport Management System (TMS) is to manage the whereabouts of goods as they leave the warehouse (i.e., have been shipped). The number of shipments per day also depends on the number of truck dispatches managed by the Transport Management System, and coordinating both WMS shipment schedules and TMS dispatches is essential for smart logistics.
What does it mean to implement a WMS exclusively for warehouse management?
In distribution warehouses, the key to improving operational efficiency is to use the most appropriate system.
The more ambiguity there is in the operational rules of a warehouse, the less likely it is that the potential of the warehouse will be fully realized. Storage areas can be meaninglessly separated from each other, or a mix of old and recent inventory can lead to workers going left and right to find the right product to ship.
Various business systems have mechanisms to track inventory and warehouse logistics. Nevertheless, a WMS is required because it can collectively manage detailed warehouse management data that cannot be compensated for by individual systems.
Main functions of the WMS
This section describes the main functions of the WMS. Please check each heading in place of the table of contents, starting with the section that pertains to your company’s needs.
Shipping and Receiving Management
Supports incoming and outgoing product shipments. By scanning the bar code of incoming products, they are recorded as inventory in the system. The system provides optimal storage location instructions based on multiple criteria, including the number of products in stock by date of receipt, shipping schedule for each product, warehouse availability, and product classification.
When a shipment is made, instructions are sent to the picking supervisor regarding the storage location and the number of pieces to be picked. If multiple products are to be picked, instructions are sent to the person in charge of picking to ensure the smoothest possible travel route based on the storage location in the warehouse.
Inventory Control
The WMS manages inventory by date of receipt, whereas other business management systems often only track total quantity. For items with predetermined expiration dates, shipping instructions are given in order of oldest to newest. For in-house products, this can also be used as material for planning sales plans, such as selling items that are nearing their expiration date as bargain items.
inventory control
Before the introduction of WMS, taking inventory was a time-consuming and difficult task. After the introduction of WMS, inventory can be completed simply by scanning barcodes.
The WMS automatically checks each product and storage location for verification, which is quicker than a visual check, and even difficult-to-understand information such as the date of arrival can be smoothly verified via the WMS.
Location Management
Control the storage location of products in detail. The storage location can be managed in detail, such as which area, what shelf, and how many shelves. While it would be impractical and time-consuming to do this manually, a WMS can provide detailed instructions on storage locations and keep track of them. Detailed location management leads to faster picking speed during shipping.
Billing Management
For mail-order orders, a delivery invoice printed with the product name, quantity, and total amount is packed with the product. Billing management is also performed automatically at the timing of shipment instructions, and the settlement of accounts (contacting credit card companies, printing transfer forms, etc.) is based on the designated payment method.
For BtoB, it is possible to manage billing information for each business partner and bill them on a specified date.
Form and label issuance
The system also supports the issuance of forms and labels to take over the status of products that have changed during warehouse operations (e.g., the number of remaining stock per box, etc.). Inventory can also be smoothly reflected when items are removed as samples or when items are found to be defective.
7 benefits of implementing a WMS
The WMS has a variety of functions, and this section summarizes the benefits of utilizing these functions.
1. drastically reduces work errors caused by human factors
Work in a warehouse is a series of simple, repetitive tasks. It requires endlessly checking incoming products, directing and instructing them to their assigned storage locations, and checking the quantities of large groups of products.
Reading barcodes with a handheld scanner is a simple and repetitive task, but it is less prone to errors than visually rechecking or inputting data into a control chart. By eliminating errors and the time and effort required for checking, it can lead to increased efficiency and significant cost reductions in overall warehouse operations.
2. increase efficiency and automation of each operation
In large warehouses that effectively use IT, incoming boxes are placed on roller conveyors and automatically transported to the desired storage location.
Some warehouses have achieved a high degree of automation by linking barcode scanners attached to conveyors to the system, which switches the destination of the roller conveyors.
3. maintain optimal inventory management operations
Inventory management requires information on the number of storage spaces in the warehouse, the number of items stored in each space, and how the space is currently being used. only a few people who are familiar with the structure of the warehouse and are involved in the daily movement of inventory.
The WMS eliminates the need for individualized operations and helps everyone involved in warehouse operations to achieve the same results.
4. efficient staffing and workforce
The frequency of shipping and receiving varies depending on the product. Although more personnel should be assigned to the receiving/shipping of products that are frequently in and out of the warehouse, there is a risk of inefficient staffing if the warehouse is not kept abreast of the movement of products in and out of the warehouse.
The WMS simplifies warehouse operations and eliminates the need to differentiate personnel based on experience. It also makes it easier to secure personnel during peak periods, such as through the use of short-term part-time workers.
5. real-time management of inventory and logistics in the warehouse
Real-time inventory counts and actual receipt/issue of each product can be monitored.
If the WMS is connected to the company network, the status of even distant warehouses can be listed together. The information can be used in a variety of ways, but it can also be useful for improving the accuracy of operations in other departments, such as planning campaigns or determining the expected financial results based on year-end inventory count forecasts.
6. easy to ensure and monitor traceability in the warehouse
Since anyone can quickly identify available space in the warehouse, flexible use of space can be made immediately, such as reserving storage space for products that have been received in greater numbers or reallocating products with fewer shipments to spaces further in the back of the warehouse.
7. increase in customer satisfaction
There are a wide variety of businesses that use warehouses, some B-to-C, some B-to-B. Whatever the type of business, a company that can maximize the storage capacity of its warehouse and quickly ship goods in and out of the warehouse will be a reliable partner for its customers, and the use of a WMS will improve customer satisfaction by providing better service in its own warehouse.
Disadvantages of WMS implementation
While a WMS can be expected to offer many benefits, there are also issues that should be kept in mind when implementing it.
In-house training on the new system
The most important task after system implementation is to ensure that the new way of working is thoroughly implemented in the field.
Furthermore, the new business operations will have a far-reaching impact not only on the warehouse operations, but also on the buyers who direct incoming shipments, as well as those in charge of product sales planning and campaigns. The first priority, of course, is to ensure that day-to-day warehouse operations are transferred to the new system without delay.
In parallel and in stages, other departments will be informed of the benefits of the WMS and how to use it. Stumbling at this point may give the impression that the WMS implementation is a failure, without understanding the value of the system.
Increase in system costs, including installation and operating costs
Naturally, there is a cost involved in implementing a new system. Whether this cost is considered large or small depends on whether the cost-effectiveness is commensurate with the investment. Although estimates should have been made in advance, it is necessary to periodically verify whether the effects are being obtained as expected.
Points of introduction to minimize disadvantages
It is important to understand the key points to minimize the disadvantages as described in the previous section.
Share benefits from employees who know the system well
Many front-line employees and managers may take pride in the fact that they have solved problems by devising various solutions and have done so successfully.
The more self-confident a person is, the more likely he or she is to have a negative image of the new top-down approach. Conversely, by having such people who are highly motivated and have on-site influence on the business on your side, they will take the initiative in driving business reforms after the introduction of the new system.
For example, it is effective to ask them to participate in the system requirements definition review meetings to the extent that it is reasonable for them to do so. Even if they are unable to attend, share the minutes of the meeting, and if they have any feedback, have them report back to you by e-mail or other means so that you can raise their awareness of their involvement in the process.
It is also effective to ask for suggestions on features you want in the field and suggestions on how to make the system easier to use. Sharing with not only the warehouse floor, but also with buyers, marketing, and other departments that have a relationship with the warehouse, the challenges faced by the floor, areas that will be made easier by the system, and examples of how the system can be used, will increase interest in and expectations for the system, and will ensure smooth acceptance of the system after implementation.
Creating manuals and conducting study sessions, etc.
At sites where warehouse operations are actually conducted, it is advisable to actively create and distribute work manuals for WMS use and hold study sessions for each work section.
Training plans and on-the-job training should be conducted mainly with on-site personnel who have shared information in advance, so that explanations can be tailored to the work and smoothly permeate the field. Study sessions should not be held once, but multiple times.
New questions may emerge as you actually perform the work. You may also find problems or effective improvements that you may have missed. It is also important to frequently gather feedback and questions in the early stages of implementation to avoid imposition or throwing everything at the system, and to present an improvement plan.
Lowering the cost of implementing a WMS
Among WMS products, there are differences in functions and suitability for different types of businesses. It is important to have a clear purpose for introducing a WMS and to determine which product is necessary for your company. Here, we focus mainly on cost and flexibility of construction, and introduce points for selecting a product that suits your company without waste.
Select a system that meets your company's needs
In order to identify the right WMS product for your company, it is important to clarify the purpose of implementation.
Choose a system not because it has many functions or is inexpensive, but because it meets your objectives and can meet your future needs. Even if the price at the time of introduction is a little high, a WMS that meets your needs will allow you to recoup your investment costs in a short period of time.
Are you focused on implementation and management costs? Do you value freedom of construction? Also consider such things as
The implementation of the system also entails high hardware costs and operating costs such as maintenance.
Cloud-based WMSs that utilize the Internet are also emerging as a solution to this problem. The cloud-based system does not require hardware or operational costs, thus greatly reducing initial costs.
On-premise WMSs, on the other hand, have the advantage of offering a much higher degree of freedom in system construction, although the installation and operation costs are higher. There are also packaged WMSs that are suitable for those who are concerned about operating in the cloud but want to keep costs as low as possible.
▼ Various types of WMS, including cloud, on-premise, and packaged, are also discussed in more detail in this article.
Explains the advantages of WMS (Warehouse Management System) and how to choose one! In-depth comparison of the latest 10 WMS products, including the company with the No. 1 market share
Let's introduce the best WMS for your business!
Here are some tips to help you choose the best one from the many WMS products available.
Understand the differences in WMS functionality between products
It is important to share objectives before selecting products.
Each WMS product has different features. Compare the functional overview of as many WMSs as possible, and refer to case studies to narrow down the candidates that meet your objectives.
Many WMS vendor sites accept free information requests. Some sites require you to register your company name and the name of your contact person, but you may want to do so to obtain in-depth information on customizability and other aspects of the product. News sites that introduce logistics-related issues and initiatives may also introduce new WMS products as relevant information.
Compare multiple products to find the right one for your company’s purposes.
The key is to select a company that can propose a system that meets your needs.
Many business systems delivered to companies can be adjusted to meet their needs and add optional features. On the other hand, cloud-based systems, which are price-driven and less customizable, are also attracting attention.
Some on-premise products also offer lower prices in exchange for being packaged products that cannot be customized. Selection of candidate products and actual implementation is done in consultation with the vendor handling the WMS. Selecting a vendor that can make proposals that meet your company’s needs is also an important process in selecting a WMS that can be used.
Aiming for more convenience, such as linking with other systems and increasing the number of locations in a short period of time.
WMS is a flexible system that enhances the potential of warehouse operations.
A WMS with excellent traceability will expand the scope of your warehouse operations. Taiyo Kogyo’s “Tent Warehouse” is recommended for handling busy periods and building temporary bases. The Tent Warehouse is low-cost, has a short construction period, and is highly durable. To make even more effective use of the flexible system environment, consider using a tent warehouse that supports warehouse operations from the hardware side as well.
Tent Warehouseへの
Contact us
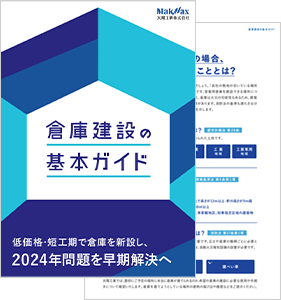
What you need to know when building a warehouse
We packed it all in.
Clues to solving the 2024 problem
I want to build a warehouse in an economical way.
Which type of warehouse should we build?
I want to learn the basics of warehouse construction anyway.
I'm concerned about the 2024 problem, but I don't know what to do about it.
Related Articles
- TOP>
- Taiyo Kogyo Column>
- A management system that solves the problems of logistics warehouses [What are the advantages and disadvantages of WMS implementation?