Taiyo Kogyo Column
What is WMS (Warehouse Management System), the key to logistics efficiency?
Have you heard of WMS, which is being increasingly introduced in the logistics industry?
WMS is a system that can optimize operations by centrally managing logistics, worker movement, and product status within a warehouse.
This article describes the WMS in detail, focusing on basic knowledge and each function.
Basic knowledge of WMS
WMS (Warehouse Management System) is a type of system software called “Warehouse Management System” in Japanese.
This system is introduced to optimize the movement of goods in a warehouse, or “in-warehouse logistics,” and to increase the speed while improving the accuracy of overall operations. The system is actually introduced and utilized in various distribution warehouse sites, including raw material warehouses, parts and product warehouses in the manufacturing industry, retail and mail-order businesses, and EC product warehouses.
WMS is increasingly offered as a cloud-based service, which has become mainstream in recent years.
The WMS will be discussed in more detail in the next chapter.
What the WMS can achieve
Let’s take a look at exactly what role the system actually plays in optimizing the logistics in your warehouse when you use a WMS.
Inventory management can be optimized.
The WMS functions as a centralized management system to streamline a series of warehouse operations such as receiving, storage, picking (retrieval), packing and shipping.
This enables thorough optimization of areas that were ambiguous or left to the discretion of on-site personnel prior to the introduction of the WMS, and helps to maintain appropriate inventory levels after optimization.
Allocation of labor resources can be optimized
Once the WMS is in place, workers can also use the guidance from the WMS to pick multiple items in a series of steps while moving along the optimal route in the warehouse and placing inventory where it should be placed.
Improved overall work efficiency reduces work time and errors, leading to optimization of labor resources.
Real-time and accurate inventory and logistics status
The WMS enables real-time and accurate monitoring of detailed warehouse logistics activities, such as which products have been shipped and how many have been shipped, how many are currently scheduled for picking, and which products are in the hands of workers at any given moment.
This centralized management is done in complete real-time, leading to an accurate and unmatched understanding of inventory counts, which enables efficient sales by avoiding miscommunication and lost opportunities when handling products through multiple sales channels, such as physical stores and e-commerce, for example.
Traceability can be ensured in the warehouse.
Under a WMS, workers scan product barcodes at every stage of the logistics warehouse process, including receiving, inventory storage, picking, distribution processing, issuing forms, shipping, and inventory.
Therefore, it is possible to track the location and status of goods in detail, and no matter how much the goods have been moved in a short period of time, the current location and status can be immediately confirmed. For example, if the system is left to the discretion of the workers on site, it is possible to avoid such misunderstandings as worker A thinking, “Product 00 has just been moved to XX, so it should still be there,” when in fact worker B has immediately moved to another location to inspect the product.
Can lead to improved customer satisfaction
The effects of implementing a WMS, such as those described above, can lead to appropriate inventory management, receiving and shipping operations, and ultimately to improved customer satisfaction through the provision of high-quality services.
Main functions of the WMS
Let’s take a look at the specific functions that make the role of the WMS, as described in the previous section, possible.
Although there are differences in the detailed specifications of WMSs among manufacturers and service providers, we will focus on the features commonly included in general WMSs.
Inventory Control Functions
The system centrally manages information such as when each item was received, where and how many items are stored, product lot information, and detailed information such as expiration dates for items with expiration dates.
Receiving management function
The warehouse will support a series of operations in which incoming goods will be stored at a predetermined location (location) after receiving operations.
At the time of receipt, for example, the barcode reading can be used to detect differences from the planned quantity or to check the expiration date.
Location Management Functions
The system manages the detailed location of all products in the warehouse, such as which floor, which area, which shelf, and how many shelves. This information streamlines all operations, including picking in the back-end process.
Shipment Management Functions
When shipping instructions arrive at the system, the system sends appropriate instructions to the picking operator’s terminal in order to ship the required number of items from the designated location, and supports a series of processes, including movement routes, so that the items can be packed and shipped according to a predetermined procedure.
Inventory Control Functions
Under WMS operation, even during inventory, workers do not visually check each item, but rather read it with a handy scanner.
In addition, in the unlikely event of a discrepancy between actual inventory data and theoretical inventory data registered in the WMS due to scanning omissions or other reasons, the system can automatically detect the situation and alert the operator or manager.
Billing Management Functions
This function is used to manage invoicing for each product.
Preconfigured settings can also be used to determine when data should be passed to invoicing, and to automate the calculation of various costs such as freight and labor charges.
Form and label issuing function
In warehouse logistics, it is common to issue forms and labels for each product status (status) for workers to visually check and scan, and to attach or insert the labels to the products.
The WMS enables accurate and prompt issuance, leading to more efficient operations related to forms.
What is the difference between a WMS and a "core system"?
One of the most commonly utilized systems in the logistics industry, as well as WMS, is the core system.
What is the core system?
Core systems are the business systems that are fundamental to the way a company operates its business.
Main differences between WMS and mission-critical systems
Core systems mainly automate and support the processing of various operations in each business field, such as sales management, inventory control, and accounting, and can also update and monitor inventory status in real time, just like a WMS. However, like a WMS, it only keeps track of inventory counts and does not support detailed logistics operations such as receiving, shipping, picking, and so on.
What is the difference between a WMS and an "inventory management system (SMS)"?
One type of system software that is often mentioned alongside WMS (Warehouse Management System) and is often confused with WMS (Warehouse Management System) is “Inventory Management System.
Let’s review what differences there are between a WMS and an inventory management system.
Some providers refer to a WMS as an inventory management system, while others have released products that integrate the functions of a WMS and an inventory management system. This section focuses on the original roles of WMS and inventory management systems.
What is an inventory control system?
A Stock Management System is basically a system for managing a wide range of detailed inventory information, such as delivery movements outside the warehouse and the status of orders before they are received.
Main differences between a WMS and an inventory control system
Inventory management systems, for example, manage the movement of which product arrived at Warehouse A, how many lots arrived, when and how much was shipped, etc. However, “detailed location movement and work flow within a warehouse,” as in a WMS, is basically outside the scope of the system.
What is the difference between a WMS and a "shipping management system (TMS)"?
Similar to WMS and inventory management systems, a delivery management system is a type of system software used in logistics.
Let’s understand the differences here as well.
What is a delivery management system?
The Transport Management System (TMS) is a system for managing items such as the movement of goods after they leave the warehouse and the time and condition at which they arrive at their destination.
Main differences between a WMS and a shipping management system
The delivery management system also does not manage detailed location and status in the warehouse like a WMS.
While WMS is mainly responsible for “receiving management,” “inventory management,” and “shipment management,” the delivery management system is responsible for “dispatch management,” “progress management,” and “performance management” during delivery.
What is the difference between a WMS and an "Order Management System (OMS)"?
The last system software commonly used in logistics is the Order Management System.
What is an order management system?
The Order Management System is a system for managing categories from orders to inventory.
Main differences between WMS and order management systems
While a WMS centrally manages logistics and status movements within a warehouse, an order management system monitors the status of customer orders, compares them with warehouse inventory, and ties them together (secures products).
Points to keep in mind when implementing a WMS
This presentation will provide information on the cautions and issues that are likely to arise in the field when implementing a new WMS.
It is important to carefully consider these points in advance when considering the introduction of the system, and to maintain on-site operations before introducing the system.
New costs for WMS implementation, and it takes time to stabilize and optimize operations
In addition to initial and monthly installation costs, the introduction of a WMS can result in decreased work efficiency due to confusion over staffing and other factors, and consequently increased personnel costs until operations can be optimized within the company.
For example, immediately after the introduction of a WMS, there may be a lack of understanding of the system’s role and what it can achieve, and the existing staff may also perform tasks that can be done by the WMS individually, resulting in duplication of checking work.
Need to train and instruct employees and workers
To provide education and guidance on how to operate the WMS, it is necessary to have a person in charge who has a thorough understanding of the WMS specifications and the work to be performed under the WMS operation to educate the staff at the site.
In addition, there are human resource costs associated with training, such as training on-site instructors to train new employees on the system.
Please consider Taiyo Kogyo's "Tent Warehouse" in conjunction with the review and optimization of warehouse logistics.
This article focused on the features, what can be achieved, and functions of WMS, software for optimizing warehouse logistics and human resources.
An increasing number of companies are introducing WMS and other management systems such as SMS, TMS, and OMS, as described above, and are working to optimize overall logistics operations by utilizing mutual collaboration.
With regard to the review of warehouse operations, we highly recommend the use of “tent warehouses” in addition to the adoption of these systems.
The tent construction method is a low-cost, quick-construction method that can be used to build warehouses and cargo handling areas with sufficient durability, and can be adapted for rapid expansion and relocation as part of warehouse operation efficiency.
Taiyo Kogyo offers a variety of products that can be used at logistics sites, including tent warehouses and other system buildings that also have short construction periods.
Click here for a list of Taiyo Kogyo Corporation’s products and services, or click here to request information materials.
https://www.tentsouko.com/
Before introducing a WMS, carefully consider and plan its introduction based on your company's situation and needs.
WMS (Warehouse Management System) is a software system that can effectively and centrally manage the movement of goods and people in a warehouse and optimize the sequence of flow in a warehouse to improve work productivity.
We hope you will consider the features and benefits described in this article and find the best system for your business.
Tent Warehouseへの
Contact us
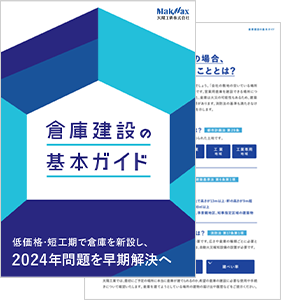
What you need to know when building a warehouse
We packed it all in.
Clues to solving the 2024 problem
Recommended for
I don't know where to start in building a warehouse.
I want to build a warehouse in an economical way.
Which type of warehouse should we build?
I want to learn the basics of warehouse construction anyway.
I'm concerned about the 2024 problem, but I don't know what to do about it.
Related Articles
- TOP>
- Taiyo Kogyo Column>
- What is WMS (Warehouse Management System), the key to logistics efficiency?