Taiyo Kogyo Column
How to organize and layout an efficient warehouse? Explanation of key points to 6 steps of design
Optimizing layout is essential for efficient warehouse operations.
We want to increase efficiency.”
We want to increase storage efficiency.”
I don’t know how to design the best layout.”
If you are experiencing these problems, please refer to this article to design an appropriate layout. This article will explain the five benefits of reviewing the layout of your warehouse, as well as specific design procedures.
Tent Warehouseへの
Contact us
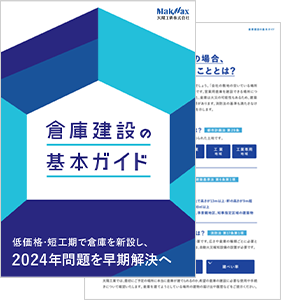
What you need to know when building a warehouse
We packed it all in.
Clues to solving the 2024 problem
Recommended for
I don't know where to start in building a warehouse.
I want to build a warehouse in an economical way.
Which type of warehouse should we build?
I want to learn the basics of warehouse construction anyway.
I'm concerned about the 2024 problem, but I don't know what to do about it.
Related Articles
- TOP>
- Taiyo Kogyo Column>
- How to organize and layout an efficient warehouse? Explanation of key points to 6 steps of design