Taiyo Kogyo Column
Detailed explanation of warehouse construction costs|From market prices by type and structure to how to keep costs low.
According to statistics on construction starts in FY2022, the national average unit price per tsubo for warehouses is approximately 450,000 yen. In addition, the cost of warehouse construction is on an upward trend due to soaring material and labor costs. Therefore, it will be necessary to select an appropriate warehouse structure in line with the purpose of warehouse construction, and to keep construction costs as low as possible.
This article will discuss specific ways to reduce the cost of warehouse construction, starting with construction methods and cost quotes for different types of warehouse construction. It is important to understand that cost quotes are only a guide and that prices vary depending on the type of warehouse and its location.
Tent Warehouseへの
Contact us
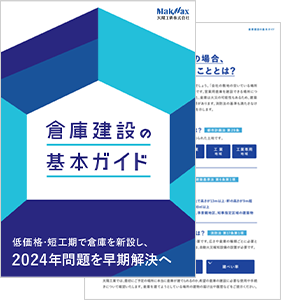
What you need to know when building a warehouse
We packed it all in.
Clues to solving the 2024 problem
Recommended for
I don't know where to start in building a warehouse.
I want to build a warehouse in an economical way.
Which type of warehouse should we build?
I want to learn the basics of warehouse construction anyway.
I'm concerned about the 2024 problem, but I don't know what to do about it.
Related Articles
- TOP>
- Taiyo Kogyo Column>
- Detailed explanation of warehouse construction costs|From market prices by type and structure to how to keep costs low.