Taiyo Kogyo Column
Basics of Warehouse Construction: Explanation of Features, Merits, and Demerits of Each of the Four Types of Warehouse Construction, as well as Construction Examples
When planning a logistics network, “optimal use of warehouse architecture” plays an important role in improving operational efficiency and optimizing logistics. However, selecting a warehouse that meets your objectives is difficult. Understand the characteristics of warehouses and select the most suitable warehouse.
This article describes the four main types of warehouse construction: conventional, tent warehouse, prefabricated warehouse, and system warehouse, for those who are planning to build a warehouse.
Tent Warehouseへの
Contact us
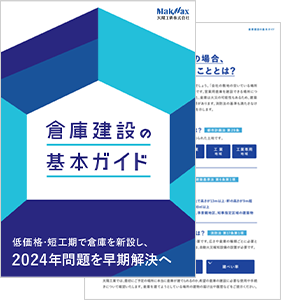
What you need to know when building a warehouse
We packed it all in.
Clues to solving the 2024 problem
Recommended for
I don't know where to start in building a warehouse.
I want to build a warehouse in an economical way.
Which type of warehouse should we build?
I want to learn the basics of warehouse construction anyway.
I'm concerned about the 2024 problem, but I don't know what to do about it.
Related Articles
- TOP>
- Taiyo Kogyo Column>
- Basics of Warehouse Construction: Explanation of Features, Merits, and Demerits of Each of the Four Types of Warehouse Construction, as well as Construction Examples