Taiyo Kogyo Column
What is a new warehouse that can be additionally built, reduced in size, or demolished in a short period of time with a short amortization period?
Table of Contents
1. Logistics Management Department, Machinery Manufacturing Company M
2. assignment
– We want to pull materials from our external warehouse, but we can’t ignore the risk of expanding our warehouse…
– Key Points of the Assignment
3. resolution
– Key Points of Solution
– The simple structure of the warehouse maintained excellent warehouse performance, while construction costs were cut by 40% from the conventional cost!
We want to pull materials from our external warehouse, but we can't ignore the risk of expanding our warehouse...
Key Points of Solution
Tent Warehouseへの
Contact us
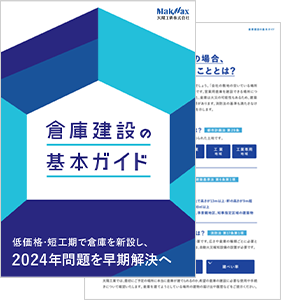
What you need to know when building a warehouse
We packed it all in.
Clues to solving the 2024 problem
Recommended for
I don't know where to start in building a warehouse.
I want to build a warehouse in an economical way.
Which type of warehouse should we build?
I want to learn the basics of warehouse construction anyway.
I'm concerned about the 2024 problem, but I don't know what to do about it.
Related Articles
- TOP>
- Taiyo Kogyo Column>
- What is a new warehouse that can be additionally built, reduced in size, or demolished in a short period of time with a short amortization period?