Taiyo Kogyo Column
No piling work is required even in soft ground! How to build a warehouse inexpensively even in waterfront areas | Tented Warehouses
2021.07.12
Did you know that the strength of the ground determines the buildings that can be built on it? When building on low-strength ground, such as in seaside areas, the ground may not be able to withstand external forces such as earthquakes or its own weight, and may settle. Therefore, when building on soft and soft ground, it is necessary to construct pile foundations for reinforcement, which can be very costly.
In recent years, more and more soil contaminants have been discovered through voluntary inspections during excavation work, etc. In April 2019, the Soil Contamination Countermeasures Law was revised, tightening construction standards for facilities that handle specified hazardous substances.
In this article,
- Construction Considerations in Areas with Soft Ground
- Construction Considerations for Areas with Soil Contamination Concerns
- Points to keep in mind due to the revision of the Soil Contamination Countermeasures Law
In addition, we will explain the “Tent Warehouse,” which is attracting attention as an effective alternative to conventional construction under specific conditions such as those described above.
Please take a look.
Table of Contents
1 Points to keep in mind in areas with soft ground
2 Points to keep in mind in areas where soil contamination is a concern
3 Points to keep in mind due to the revision of the Soil Contamination Countermeasures Law
4 New option of “Tent Warehouse
5 What is a tent warehouse?
6 Advantages of Tent Warehouses
7 Taiyo Kogyo’s tent warehouse is recommended.
8 Advantages of Taiyo Kogyo’s Tent Warehouses
9 Conclusion
Points to keep in mind in areas with soft ground
Reference: Foundation construction site under construction (Photo AC)
What is a soft ground area?
Soft ground is ground composed of soft clay or loose sand. The higher the water content, the softer the ground. If a building is constructed on this type of ground, the weight of the building will cause the water in the soil to escape, and the building will sink by the amount of water.
Such soft ground is often found in waterfront industrial parks, reclaimed areas, and areas where there were ponds or swamps.
Pile foundation work required
Whenever a factory or other building is constructed on soft ground, it is necessary to install pile foundations. This is done by driving foundation piles that reach deep into solid ground that is strong enough to support the building. There are various types of foundation piles, but in cases where the ground is particularly soft or where large buildings are to be constructed, such as in coastal industrial parks or reclaimed areas, “steel pipe piles” are used, which can be driven to a depth of about 30 meters.
Significant costs.
When constructing factories and other facilities in areas with particularly soft ground, such as coastal industrial parks and reclaimed areas where the ground is weak, it can cost as much as 10 million yen just to drive steel pipe piles. However, it is difficult to reduce the cost by shortening the construction period or lowering the grade of the foundation work, because it is an area where legal standards are set because it could affect human lives if the building sinks or collapses.
Points to keep in mind in areas where soil contamination is a concern
See also: Muddy(Photo AC)
What are areas of soil contamination concern?
Areas where facilities that handled hazardous specified substances were constructed, such as former gas and chemical plants, are most likely to be filled with contaminants. Also, areas where industrial waste disposal sites have been reclaimed tend to contain buried contaminants.
Appropriate after-action will be required.
When a company voluntarily investigates the soil contamination status of a proposed construction site, it is called a “voluntary investigation. If a voluntary survey reveals soil contamination, the company must take appropriate measures, such as reporting to the designated agency.
Points to keep in mind due to the revision of the Soil Contamination Countermeasures Law
Notification of change of form is required
The Soil Contamination Countermeasures Law was revised in April 2019. As a result, when excavation work of 50 cm or more is conducted on land of 900 m2 or more for the construction of a factory, etc. where specified facilities using hazardous substances are to be installed, it is now mandatory to submit a notification to the prefectural governor, etc. for the change in the land’s shape. Since the standard before the revision was 3,000 m2, the scope of application has been greatly expanded.
Careful preparation is required for notification, as many attachments must be prepared, including detailed drawings, certificates of registered matters, and land use history.
Difficult to continue business during investigation.
If, as a result of the notification, the prefectural governor, etc. orders you to conduct a soil contamination survey, you must comply with the order as soon as possible. In such cases, construction cannot begin until the results of the investigation are reported and approval is granted, so it is necessary to assume that there may be a temporary suspension of the project at the planning stage.
In some cases, the start of construction is prohibited.
If the results of the investigation indicate that the designated criteria for health hazards have been exceeded, measures such as removal of contaminants or a general prohibition on landform changes will be ordered. In some cases, the construction period may be significantly extended or even cancelled.
A New Option: "Tent Warehouses
Tent warehouses are now attracting attention as a new option to solve these problems. Tent warehouses can solve all of the above-mentioned risks, such as increased costs, excavation work, cumbersome notification, and temporary suspension of business.
What is a tent warehouse?
Tent warehouses are warehouse structures built on tents, which are constructed by assembling a lightweight metal steel frame and covering it with a membrane material. Tent warehouses, which take advantage of the features and characteristics of membrane materials, have a number of advantages and are used in a variety of situations.
Advantages of Tent Warehouses
Significant cost reductions
As mentioned earlier, when constructing a factory or other facility on soft ground, it costs 10 million yen just to drive steel pipe piles. With tent warehouses, even if the ground is weak, there is no need to drive piles, and installation can be done simply by improving the ground to a depth of 50 cm to 100 cm. Since the cost of ground improvement is in the order of 1 million yen, a tent warehouse can cut costs by a factor of 10 or more compared to conventional methods.
No excavation work required
Compared to conventional construction, tent warehouses are lightweight and can be constructed with a foundation specification without any excavation at all. No excavation is required, even in ground that may contain contaminants. While a typical warehouse cannot be built on ground with a bearing capacity of less than 30k N/m2, this is possible with tent warehouses.
No need to submit a change of form report and no need to worry about business interruption
We have reported that due to the revision of the Soil Contamination Countermeasures Law, factories and other facilities that handle hazardous substances with an area of 900 m2 or more and that require excavation work of 50 cm or more must submit a notification of change in the form of the building. Tent warehouses do not require excavation work of more than 50 cm unless the ground is soft, and can be installed on a foundation, so there is no need to submit a time-consuming change of structure notification even if the area is more than 900 m2.
In addition, the project can proceed on schedule because there is no possibility of business interruption due to soil contamination investigations.
Taiyo Kogyo's tent warehouse is recommended.
There are many different types of tent warehouses, but we recommend the membrane-structured “tent warehouse” made by Taiyo Kogyo Co. The disadvantages of ordinary tent warehouses are eliminated by a special membrane material that utilizes photocatalytic technology.
Advantages of Taiyo Kogyo's Tent Warehouses
Maintain a clean space
Tent warehouses are mainly used to store products and materials, so the inside of the warehouse must be a clean space. Taiyo Kogyo’s special membrane material coated with titanium dioxide can maintain a clean space inside the warehouse because dirt adhering to the surface of the membrane material is decomposed and removed on its own.
Reduce room temperature rise
During the summer months, when temperatures rise, the maximum temperature in a typical warehouse can rise to 40°C-45°C. This is a level that is dangerous to the human body. Membrane tent warehouses can lower the temperature by approximately 3.5°C compared to a typical straight structure tent warehouse, thus protecting the health of the workers.
Tent Warehouseへの
Contact us
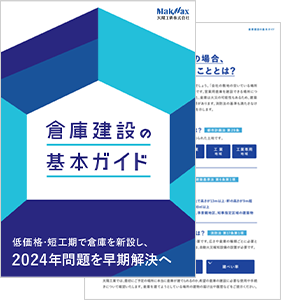
What you need to know when building a warehouse
We packed it all in.
Clues to solving the 2024 problem
Recommended for
I don't know where to start in building a warehouse.
I want to build a warehouse in an economical way.
Which type of warehouse should we build?
I want to learn the basics of warehouse construction anyway.
I'm concerned about the 2024 problem, but I don't know what to do about it.
Related Articles
- TOP>
- Taiyo Kogyo Column>
- No piling work is required even in soft ground! How to build a warehouse inexpensively even in waterfront areas | Tented Warehouses