Taiyo Kogyo Column
Is it time for repairs or renovations to be made to your warehouse roof?
Because warehouse roofs are required to perform a variety of functions, they must be closely monitored for deterioration and damage, and appropriate repair and renovation must be undertaken.
This article provides information on warehouse roofs, when repair and recovery is needed, and recommended repair methods.
Functions required for warehouse roofs
The roof is an extremely important part of a building, but it is especially so in a warehouse. Warehouses are especially important because of the work that goes on inside and the valuable goods that are stored there. When considering a warehouse renovation, it is advisable to understand the function of the roof in the first place.
Waterproof, windproof
Naturally, the first step is to shelter from the wind and rain. Japan has a rainy season and typhoon season every year. If the cost of waterproofing and windproofing is ignored, water leakage and wind damage will soon occur. Performance here is paramount.
Related article: ” Typhoon damage can also be mitigated! What’s the Appeal of Tent Warehouses? “
sound insulation
An often forgotten feature, but essential when using a facility for business purposes, is sound insulation. Forklifts in a warehouse can generate considerable noise, and machinery noise can be loud in a factory. When considering the surrounding environment, sound insulation should also be taken into account.
fire resistance
Warehouses above a certain size are required by the Building Standard Law to be fireproof or quasi-fireproof. (Ministry of Land, Infrastructure, Transport and Tourism, ” Outline of Building Standard Law System,” 2009)
Not only by law, but in Japan, where winters are dry and buildings are close to neighboring structures, fire resistance is a feature that must be taken into consideration.
light-generating property
Although light harvesting is not a common requirement for warehouse roofs, it is actually a feature that can have significant benefits.
A bright environment increases the visibility of workers in the warehouse. It is also said that brightness can also improve people’s moods and increase productivity. It also improves work efficiency, and if the structure is designed to let in more natural light, it will directly lead to a reduction in electricity costs for lighting.
Thermal Barrier
In the summer, temperatures inside warehouses can rise dangerously high, sometimes reaching 40-45°C (104-95°F). The main cause of high temperatures is said to be the roof, making thermal insulation an indispensable feature.
*For more information, please refer to this article.
What is “heat control” and specific improvement measures for logistics warehouses and factories?
Warehouse Roof Lifespan and Timing of Replacement Repair/Renovation
What is the life expectancy of a warehouse roof, which is required to be multi-functional?
Generally speaking, most warehouse and factory roofs are “folded half roofs” and “corrugated slate”.
Image of “half roof”
Image of “corrugated slate roof”
Depending on the environment and materials, each is said to have a lifespan of 15 to 20 years. In other words, large-scale repairs, such as total re-covering, are necessary every 15 to 20 years.
Consider covering or replacing the roof after 20 years of age.
- Cover construction :Cover the top with new material
- Roof replacement: Replace all roofing materials
In addition, warehouse roofs are easily affected by the environment due to their large area and require painting every 7 to 8 years in addition to replacement.
Especially in the case of re-roofing, the cost can run into the tens of millions of yen, and the construction period is long, sometimes as long as three months, so extensive planning is required, including time off from work.
Low-cost and short construction period "Tent Warehouse" is recommended.
It is difficult to come up with tens of millions of yen for roof maintenance or to consider shutting down a warehouse operation for several months during a construction period.
What we recommend is the renovation with “tent warehouses” of membrane construction.
If you have never considered a tent warehouse before, you may have a tendency to think that membranes are a “grotesque” or “temporary” material, but in fact, membranes have many advantages.
- No rusting, so there is little worry about water leakage, etc. due to deterioration.
- It is flexible, earthquake resistant, and even in the worst case scenario, its light weight minimizes damage.
- Its high light-gathering ability makes indoor spaces brighter and saves electricity.
- The service life is about 15 years, which is not short.
- Because of its light weight, it can also be used to create larger openings in buildings.
- The flexibility of the design also allows for appearance and comfort at the same time.
- Renovation costs are low and the construction period is short.
Membrane materials can further reduce construction costs by about 40% and shorten construction time by about 66%. This is why we recommend converting your warehouse roof to membrane material.
Image of reducing construction costs (Source: Taiyo Kogyo Co., Ltd. Advantages of introducing membrane structures)
Image of reduction in construction period (Source: Taiyo Kogyo Co., Ltd. Advantages of introducing membrane structures)
Hybrid" type offers security and peace of mind.
Even if functionally superior, the membrane is less than 1 mm thick, so security may be a concern, especially in distribution warehouses.
In such cases, we recommend the “hybrid” type, which uses membrane materials only for the roof, while the walls are constructed using conventional methods. This type of roofing system can provide security while enjoying the functional benefits of a roof.
Hybrid type image
(Source: Taiyo Kogyo Co., Ltd. Tent warehouse: Hybrid type)
Improvement of working environment by simply roofing the work area with a membrane.
Did you know that environmental improvements in the “work area,” where trucks load and unload cargo in warehouses, have recently received a lot of attention?
The poor working environment and long working hours of truck drivers in particular have become a problem in recent years, and one of the reasons for this is the environment of warehouse workplaces. The state of the work area, especially the roof, is a major factor, as there is no roof even in the rain or hot sun, and there is inadequate lighting even in the dark hours.
In response, there was news that Toyota Motor Corporation is also improving the roofs at its factory receiving and shipping workplaces company-wide.
By reviewing not only the warehouse itself but also the work area at the time of repair, you may be able to improve operations and achieve other benefits beyond your imagination.
An image of a membrane roof in a workplace
(Source: Taiyo Kogyo Co., Ltd. Tent warehouse: Open workstation)
What do you think? If you are considering repairing and renovating your warehouse or factory roof, this is a good time to consider a tent warehouse with a membrane roof.
Tent Warehouseへの
Contact us
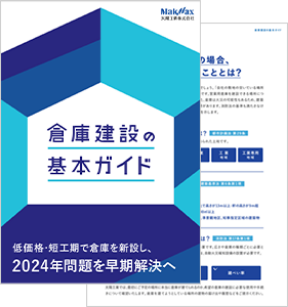
What you need to know when building a warehouse
We packed it all in.
Clues to solving the 2024 problem
I want to build a warehouse in an economical way.
Which type of warehouse should we build?
I want to learn the basics of warehouse construction anyway.
I'm concerned about the 2024 problem, but I don't know what to do about it.
Related Articles
- TOP>
- Taiyo Kogyo Column>
- When and how best to repair a warehouse roof?