Taiyo Kogyo Column
Guide to Building a Hazardous Materials Warehouse|Everything from laws and regulations to requirements, how to proceed, and means to reduce costs
Construction of a hazardous materials warehouse requires strict laws and conditions. To ensure proper understanding and success, we will explain the necessary conditions, the specific process, and tips for selecting a contractor.
In recent years, the need for hazardous materials warehouses to properly store and manage hazardous materials has increased. However, many businesses are hesitant to construct such facilities because of the strict legal compliance and conditions required. When proceeding with construction, it is essential to select an experienced and reliable contractor. Choosing a company that is familiar with laws and regulations and has a wealth of experience will help ensure smooth construction and safe operation. This article provides a wide range of explanations, from the basics of hazardous materials warehouses to the construction process, tips on how to keep costs down, and how to choose a contractor.
Click here for a free estimate and inquiry for tent warehouses! への
Contact us
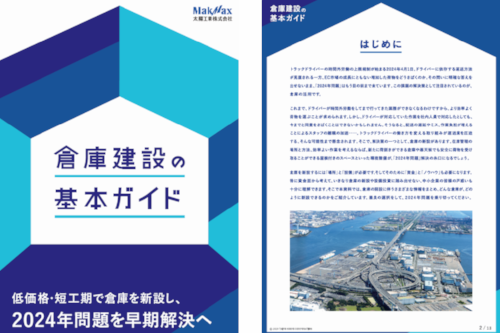
Basic Guide to Warehouse Construction download
28 pages <Recommended for the following people> ・Don't know where to start in building a warehouse ・Want to build a warehouse economically ・Don't know which type of warehouse to build ・Learn the basics of warehouse construction ・Don't know what to do about the 2024 problem
Related Articles
- TOP>
- Taiyo Kogyo Column>
- Guide to Building a Hazardous Materials Warehouse|Everything from laws and regulations to requirements, how to proceed, and means to reduce costs